Innumerable uses of polycarbonate plastic for various purposes exist and there are just so many ranges and shades of this, the black option carries its own benefits aside from aesthetics. Much of the use of Polycarbonate plastic, especially the black polycarbonate plastic, is for structural purposes. Most known for its exceptional lightweight composition and exceptional strength, black polycarbonate plastic is commonly found in applications ranging from automotive parts to electronics and construction. This article provides an in-depth analysis of the characteristics, applications, and benefits of the topic. Suppose you are a manufacturer, an engineer, or simply someone interested in advanced materials. In that case, this publication will help you understand why black polycarbonate is preferred for high-stress applications. Enjoy the guide as we go into the technical details and industrial uses of this extraordinary substance.
Understanding Black Polycarbonate
Black polycarbonate is a thermoplastic material, known for its considerable strength, fracture resistance, and thermal expansion abilities. It consists of the same basic materials as polycarbonates, which is why its manufacturing process is the same except for the dyeing process. The black color enhances the UV absorption also harmful to other colors hence black pigment is more appropriate closer to the surface. Regardless of being very light, the material is very reliable and can maintain shape under high force or temperature. Thanks to these additional features aforementioned, the high performing material of black polycarbonate has no limits for its application in the motor vehicles, electronics, building construction, and aviation and space sectors.
What is Black Polycarbonate?
Black polycarbonate is a thermoplastic with high performance and it is attractive especially because of its toughness, impact resistance and resistance to pan poker. It is composed of the condensation of bisphenol A (BPA) and phosgene, over which the polymer alters its degree of crystallinity, preparing a very reinforced and lightweight material. As mentioned earlier, such a modification may be necessary for improving the decorative effect of the polymer, as well as enhancing the polymer’s resistance to ultraviolet (UV) radiation in cases where the polymer is intended for outdoor applications.
This polymer in its natural clear state is much clearer than this structure, which is developed for the special purpose of working against any light, and it is more opaque and carries the qualities of protecting against UV polish. The materials of black polycarbonate have internal physicochemical characteristics which are high in melting temperature, low in water absorption, excellent in dimensional stability even if thermal variations exceed the limits of -40°C to 120°C or -40°F to 248°F, and, above all, high in toughness. Its toughness is high enough to withstand impacts and, for example, in protective glazing and safety shields, to be used under high stress conditions; it abides by regulations for more difficult glass.
Unique Properties of Polycarbonate Sheets
- High Impact Resistance
Polycarbonate sheets were discovered to possess extraordinary impact strength. They claim to have 250 times the strength of standard glass and 30 times the strength of Acrylic sheets. In case one needs a safety glazed or a protective barrier, this material can be advisable in such an environment.
- Thermal Stability
Cool Polycarbonate sheets can be used not only indoors but also outside, as there exist counteracting effects these sheets have on elevated temperatures. As one can observe, the polycarbonate sheets are extremely flexible and they do not expand or lose their shape within proper temperature ranges -40°C to 120°C (-40°F to 248°F), which makes the polycarbonate excellent for areas with problems of warming and cooling.
- UV Resistance
Many products of polycarbonate are gel-coated with specific ultraviolet (UV) protectants. These layers are used in some grades of polycarbonate sheets for outdoor applications to stop fading and white light issues caused by sunlight exposure. Such polycarbonate sheets, when protected from the UV light, can be expected to last for over ten years in outdoor settings.
- Light Transmission
The ultraviolet stable polycarbonate sheets can allow the introduction of light into the passive structure through up to 90% light transmission, comparable to that of glass for about 90%. They are a common sight visible in malls and can also be used for other purposes, such as skylights, greenhouses, and glass splashbacks.
- Fire Resistance
Comparison with Acrylic and Glass
Parameter |
Polycarbonate |
Acrylic |
Glass |
---|---|---|---|
Weight |
Lightweight |
Lightweight |
Heavy |
Impact Resistance |
High, ~250x stronger than glass |
Moderate, ~17x stronger than glass |
Low, prone to shattering |
Transparency |
Up to 90% light transmission |
Up to 92% light transmission |
Up to 90% light transmission |
Durability |
Highly durable and flexible |
Brittle under stress |
Brittle, breaks under impact |
UV Resistance |
Coated for UV protection |
Limited natural UV resistance |
Good, but needs additional coating |
Temperature Resistance |
-40°F to 248°F (-40°C to 120°C) |
14°F to 176°F (-10°C to 80°C) |
Extremely high, withstands higher temperatures |
Fire Resistance |
Self-extinguishing, UL94 V-0 or V-2 |
Flammable, burns with a slight odor |
Non-flammable |
Cost |
Moderate |
Low |
High |
Scratch Resistance |
Moderate, can scratch easily |
High |
Very high |
Applications |
Skylights, greenhouses, safety shields |
Displays, signage, decorative elements |
Windows, structural elements, optics |
Applications of Black Polycarbonate Sheets
Being a material that combines all of the above properties, the applications of black polycarbonate are vast across industries that require minimal flexibility of standards and high UV weather resistance. Common uses include:
- Electrical and Electronic Enclosures: It is appropriate for enclosing sensitive instruments due to excellent insulation and heat resistance ratings including retardation against spread of open flames.
- Protective Barriers and Shields: High polymer materials like black polycarbonate are suitable for such applications as machine guarding, micro-welding, and partitioning in factories, among other safety measures.
- Automotive Components: Used for making such items as headlight, taillight, mirrors, grills and interior decoration panels.
- Outdoor Signage: Can withstand harsh environmental such as harmful UV radiation and is used for advertising purposes.
- Architectural and Design Features: Used in the production of canopies, roofing and decorative lattice panels because in addition to its strength it is beautiful.
These convenient plastic materials are able to meet the requirements of different needs and sites.
Industrial Uses of Black Polycarbonate
- Electrical Enclosures: Black polycarbonate is often used for electrical boxes, because its molded insulation materials effectively separate charges, prevent arcing and resist high temperatures. The enclosers are designed in a way so, that the elements within them are protected from the environment, and from any mechanical stresses.
- Automotive Components: This material is made for producing customized elements of cars like undercarriage splash guards, anything grille-related or interior duct trims, where it has to look good and endure high stress. It works really well with cars as the temperatures they function in do not affect the material properties, hence the life of the vehicle is extended.
- Protective Machine Guards: There are two major reasons why black polycarbonate is the best material to put in the manufacturing of machine guards. One, it is not easy to break; two, it is lightweight. Those barriers perform double duty by improving health and safety aspects in the workplace without visually enhancing the boundaries.
- Optical and Security Applications: Black Polycarbonate sheet is also used as cheap, discreet-looking security glazing, and lens covers for military applications, which are so much lighter and have an optically very clear type of material. Its scratch resistance properties and adequate level of clarity also allows the use of such material in the manufacturing of optic lenses, like protective glasses, constructional face shields as well as bulletproof glazing.
- Aerospace and Defense: Since polycarbonate can withstand high temperatures and is capable of reaching extremely high temperatures once ignited, it is used to make armored glass.
Automotive Applications of Black Polycarbonate
- Headlamp and Taillight Lenses
Black polycarbonate is frequently used in the manufacturing of tail and headlamp covers. Thanks to the exceptional light response of the material, as well as heat application qualities, it performs well for a long time. Studies have found that vehicle lenses made of polycarbonate can reduce a vehicle’s weight to almost half of what it could have been if normal glass lenses were used this is approximated at 50% without any loss of distortion.
- Interior and Exterior Trim Components
Within this scope, black polypropylene also offers special advantages for dashboard, door and other interior and exterior components, which are subject to high stress. In such applications, polycarbonate endures for a longer period of time and it is not easily altered by UV rays even after direct exposure to the sun for a long time.
- Glazing and Window Elements
The use of polycarbonate in the motor vehicle industry is ever-increasing, more so in the replacement of conventional automotive glass in windows and roof systems. The lighter weight, as well as the 200 times stronger than glass enhancement provided by black polycarbonate to the reproduction of the glazing configuration, has significantly improved the mechanical performance of the vehicles.
- Under-the-Hood Components
As such, the high thermal and chemical benefits of black polycarbonate have seen its use in areas such as engine covers, air induction systems, including the control units, and electrical parts. This protects the parts and subsequently detaches the system from the harsh environment in which it may have to function.
- Protective Shields and Safety Panels
Black Polycarbonate is the best material for producing equipment that is exposed to harsh conditions, including screens like water shields and safety glasses. These are very essential in making sure no damage occurs in the normal operating lifetime of a vehicle, usually when driving as well as in cases of road accidents.
- Aerodynamic Accessories
Advantages of Using Black Polycarbonate
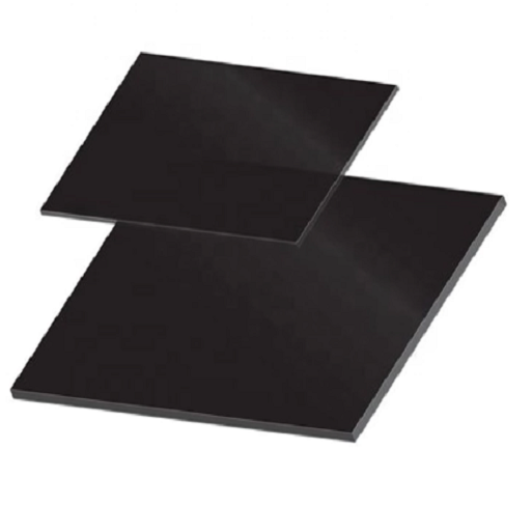
- High Impact Resistance
Typically constructed with black polycarbonate, these parts exhibit strong mechanical properties essential in automotive engineering or for the fabrication of protective sheets.
- Lightweight yet Strong
Black polycarbonate is valued because, even though it lacks the geometrical intricacies, it remains a stable shape and weighs less during processing, thus less effort is expended.
- Weather and UV Resistance
This particular material will be concerned with all weather conditions that include the direct effect of ultraviolet radiation and will serve in most of the outdoor applications for quite a considerable period of time without any maintenance.
- Versatility in Design
This can produce incredibly detailed constructions, suiting both commercial and personal markets.
- Cost-Effectiveness
Black polycarbonate combines durability, strength, and functionality, providing long-term value and reducing the need for frequent replacements.
Impact Strength and Durability
Black polycarbonate adds a high preference in practical examples, especially when relying on a hundred percent durability. This is one kind of the most rugged products engineered for the hardest applications ever built. It reportedly extends the impact tenacity of glass almost two and a half times and acrylic more than twenty-nine times, providing such ease on the willingness of the material to undergo stress without breaking. This natural toughness, conditionally outlined in black polycarbonate, enables the material to resist very intense physical behaviors such as extreme accelerations resulting from high-speed impacts, abrading caused by high loads present in moving machinery, typical of most industrial and construction environments.
Furthermore, the resistance to certain environmental conditions, such as fluctuations of the temperature, UV degradation, and attack by chemicals, doubles the product’s overall life span. Such properties make it more suited for indoor and outdoor use, especially in areas that require effective machinery that gets affected by adverse conditions. Its longer life, therefore, means more reasons for fewer maintenance requirements, and in products that are made with it, it is the best reseal possible for producers.
UV Protection Capabilities
UV protection layers of particular tropical technologies are produced so as to protect materials from the long-term exposure to ultraviolet radiation. This can be achieved through the introduction of socioelements, such as UV absorbers and stabilizers, into the materials, which help attenuate the harmful effects of radiation. Reliable information suggests that the use of UV materials helps maintain the mechanical and aesthetic characteristics of exterior materials for longer periods of operation by minimizing fading, cracking, and degradation due to exposure to UV rays. Reaching such a thorough thermal or chemical stabilization, as in the case of UV-stabilized polymers, it is possible to achieve long-life photostable conquer with no short of UV-deterioration under the sun, regardless of the humidity or rather the moisture concentration in the air. Hands are also applicable in cases where it is necessary to provide protection to elements that are damaged by environmental factors, such as those exposed to the sun. For several years. However, these application solutions entail the use of UV-stabilizers and additives along with specific limitations, which work in settings that require guaranteed suitable levels of resistance to UV radiation, such as UV-resistant coatings.
Cost-effectiveness of Polycarbonate Products
The inherent cost-effectiveness of polycarbonate products is due to their characteristics with an emphasis on the strength of the materials, the usability and applicability. In this regard, polycarbonate is able to make savings not only in terms of the issues of initial outlay and operational costs, e.g., when replaced by materials such as glass or acrylic plastic, but it also helps in cost-saving in other areas of construction because the materials are lightweight. This lightweight iser savings on the shipping charges were preserved, enabling better quality fixed constructions. Finally, polycarbonate seems less prone to damage under mechanical stress, which cuts down on repairs and replacements, thereby reducing cost over time.
Black Polycarbonate’s Role in Sustainability
Several features allow black polycarbonate to blend into sustainability paradigms. Indeed, recyclability, longevity and ease of manufacturing make it a stylish and eco-friendly edge of material sciences. Extended durability properties imply that there will be less instances where replacement of the material is necessary. Hence, wastage and use of resources is at their minimum. Besides, ability to reuse black polycarbonate means this material supports the circular economy. The manufacture of black polycarbonate is efficient in terms of energy, which cannot be said of many other hard-to-recycle products. This set of benefits promotes the use of the particular material as responsible ones are expected to be.
Environmental Impact of Polycarbonate Plastic
There has recently been a remarkable shift that has seen polycarbonate plastic reduced to almost nil decimation of the Eco resource in question. These days, most companies opt to use solar and wind energy while making black polycarbonate, thus minimizing the amount of green gases that are emitted. Besides the renewable energy networks, however, there has been another technology called catalysis that has also come into play. Catalysis is the process through which reaction efficiency is improved and as a result it becomes expensive in both raw material and energy consumption in the synthesis of polycarbonate.
Polycarbonate plastic offers significant advantage of acid resistance and chemical compatibility that are particularly useful for both short and long term applications such as automotive bumpers or consumer devices among industries. This lack of fallacy in a very highly durable material also helps in induced materials prophylaxis over any significant lifespan in use.
In addition, attention has been paid to the development of biobased polycarbonate derived from plant and polyol feedstock, particularly isosorbide. Other related technologies are aimed at using polymers made from such raw materials in order to avoid the use of resource and energy-intensive fossil fuels and at the same time retain the desired characteristics of the material. Moreover, because of how the changes that have been made contribute to the alteration, this shows the enhancement of polycarbonate plastics’ sustainability in various applications as industries tilt themselves to the principles of the circular economy.
Recycling and Reusability of Black Polycarbonate
Black polycarbonate is difficult to recycle because of the presence of carbon black that alters its color, an ingredient that can make it quite challenging for the materials to be sorted and prepared for conventional recycling processes. Where optical sorting units with near-infrared light detection are used, it is clear that it is not as effective to detect the color black. This then means that there are even instances when the recycled black polymers are easily disposed into the landfills yet they have a high recycling ability inherently.
Latest developments involve creating systems that can improve the ease of recycling black polycarbonate through materials, which include various sorting equipment and chemical remanufacturing. Development, such as the enhancement of dyes and resins with fluorescent elements, as well as the use of selective rankings, is under research for making the recyclable polymers visible to the near infrared systems. On top of that, there are chemical methods that enable the decomposition of polymers into their monomer units, thereby enabling black polycarbonate to be regenerated and reprocessed without reducing the quality of the material.
Working with Black Polycarbonate
Working with black polycarbonate becomes problematic because the optical properties of black polycarbonate are such that waste black plastic cannot be sorted through optical means at the plastic waste recycling programs. This forces the plastic waste to be recycled using specialized methods such as advanced infrared or near-infrared based sorting technologies. And as such, to effectively use black polycarbonate in production, one has to remember about such considerations as its resistance to heat and weather, which allows not only for the optimization of methods, materials and tools to be used, but also secures the minimum performance in using the product.
In order to prevent the melting or molding of the plastic black PC, careful cleaning and drying procedures such as how the raw material is handled are needed. Soil particles or moisture within the solid material can always lead to a decrease in the final product’s mechanical and superficial properties. Moreover, it is important to keep process temperatures within recommended values in order to avoid high temperature damage as well as ensure the material’s structure integrity.
As for the material, black polycarbonate has no problems with adding fillers or influence additives (glass fibers) for stiffness or impact resistance enhancement. reshaping of materials by thermal stresses can sometimes be done but requires formulation and compounding techniques that will ensure that the polymer remains homogenous and has good mechanical properties.
How to Cut and Finish Black Polycarbonate Sheets
An important aspect in handling black polycarbonate is associated with the cutting of black polycarbonate sheets such as the alignment and all the necessary tools that ensure that there are no cracks or damage to other parts. A circular saw with a fine-tooth cutting, which has a carbide edge tip, is preferable to use for cutting straight sections as it produces the best outcomes. For curves or a more complicated shape, the choice should go in favor of something like a jigsaw with a rather thin metal cutting blade. these instruments should be on their moderate speed only because a high-speed can damage the product and make the edges uneven due to melting/warping of the material along the cut line. In addition, the sheet should be properly held to minimize movement as any movement may worsen the cut in progress.
It is recommended to cover the sheets when working to protect the protective films at the edges from damage or mechanical wear. While pieces of polycarbonate are being processed, it is vital that one puts on safety eyewear as well as protective gloves because the particles may cause injury to a person.
When the cutting job is finished, seat grinding should be carried out to improve the appearance while aiding in safety. These sharp edges can be removed by using sandpapers of gradually increasing roughness, e.g., from around 120 grit to approximately 600 grit for a polished appearance. When high-quality clarity is required, particularly in the edges, a process of melting the material using a flame that is attached to a gas burner is a helpful way of polishing the edges. This last safety precaution is, however, also required because not all unwanted materials on such surfaces can be easily reached by the naked flame without causing further distortion of the material. The proportion of heat around the method and high-intensity lighting will cause changes, such as hardening or bubbling in small areas, that degrade the material. Apply it to a scrap of polycarbonate before.
Choosing the Right Thickness for Your Project
When selecting a suitable thickness of polycarbonate for a specific project, several factors need to be considered. For glass or window purposes, the regular thickness range between 4-10mm, and such levels are sufficiently high for impact resistance and visibility. The application of such systems, which involve the use of five additional sheets of polycarbonate, requires the use of thicker sections, typically in the range of 10-20mm thick, to absorb sufficient load without failure. Such applications, for example, surfaces or handrails, no matter how small they are, may have margins of safety in demanding or complex situations. For example, designing textile wall hangings or light elements usually requires only thin material, 2-3 mm max. Finally, the project site-specific loading conditions like wind, thermal expansion or contraction, as well as solar radiation, have to be projected because such aspects can contribute to changes in the properties of the material in use in the long run. The use of UV-resistant or multi-purpose polycarbonate-polyester may also be beneficial when a long-lasting solution for outdoor applications is required, out of which bi-overhaul efforts have been made to preserve the strength and general appearance of the material.
Reference Sources
-
Clarifying the Results of a Study on Black Plastics (NPR):
- Key Findings: A study initially suggested that flame retardants in black plastic kitchenware posed significant health risks. However, a correction revealed that the levels of these chemicals were far below hazardous thresholds, reducing the perceived risk.
-
Researchers Use Sunlight to Recycle Black Plastics (Resource Recycling):
- Key Findings: Researchers developed a method to recycle black plastics using sunlight or LED light. The process breaks down plastics into their molecular components, achieving up to 80% conversion efficiency with sunlight.
-
The Dark Side of Black Plastics (McGill University):
- Key Findings: Black plastics, often made with carbon black, pose recycling challenges and may contain potentially harmful substances like polycyclic aromatic hydrocarbons (PAHs). These plastics are difficult to sort in recycling facilities and often end up in landfills.
Frequently Asked Questions (FAQs)
Q: What is black polycarbonate plastic and what are its uses?
A: Black polycarbonate plastic is a durable thermoplastic known for its high impact resistance and versatility. Often used in both indoor and outdoor applications, it serves as an excellent material for DIY projects, protective panels, and various industrial uses. Its opaque finish provides a sleek appearance while blocking UV rays, making it ideal for outdoor use. Many people choose to buy black polycarbonate sheets online due to their availability and competitive prices. Whether for a sign, automotive project, or custom cut-to-size piece, this material offers a variety of options to suit your needs.
Q: How thick should my black polycarbonate sheet be for different projects?
A: The thickness of a black polycarbonate sheet can vary depending on the specific project requirements. For light-duty applications, a thickness of around 2-3mm may be sufficient, while heavier-duty projects may require sheets that are 5mm or thicker. If you are creating a sign or protective panel, consider the impact strength needed for your application. Thicker sheets typically provide superior durability and resistance to damage. It’s advisable to consult with a supplier for recommendations based on the intended use, especially if you’re looking to buy custom sizes or specific thicknesses.
Q: Can black polycarbonate sheets be cut to size for specific projects?
A: Yes, black polycarbonate sheets can be easily cut to size for a variety of projects. Many online retailers offer cut-to-size services, allowing you to request a quote based on your specific dimensions. This feature is particularly useful for DIY projects where precise measurements are crucial. Using the right tools, such as a circular saw or a utility knife, you can achieve clean edges and a smooth finish. Whether you’re building a sign, creating a protective cover, or constructing an outdoor panel, cutting polycarbonate sheets to the desired size ensures a perfect fit for your application.
Q: What are the advantages of using black opaque polycarbonate sheets?
A: Black opaque polycarbonate sheets offer several advantages, including excellent impact resistance, UV protection, and a sleek aesthetic. This tough material is ideal for both indoor and outdoor applications, making it suitable for a variety of projects. The opaque color provides privacy while still allowing for some light diffusion, which is beneficial in settings where visibility is not a priority. Additionally, black polycarbonate is lightweight yet durable, making it easier to handle and install compared to glass alternatives. Many individuals and businesses choose this material for its balance of strength and versatility.
Q: How does black polycarbonate compare to acrylic for outdoor use?
A: When comparing black polycarbonate to acrylic for outdoor use, polycarbonate generally offers superior impact resistance and durability. While acrylic can scratch more easily and may become brittle over time, black polycarbonate remains tough and maintains its integrity under various weather conditions. Additionally, polycarbonate provides better UV protection, which helps prevent yellowing and degradation over time. If you are looking for a material that can withstand harsh environmental conditions while still providing a sleek appearance, black polycarbonate is an ideal choice. However, acrylic is often more affordable and can be a suitable option for less demanding applications.