Polyoxymethylene (POM), also known as acetal or polyacetal, is an engineering thermoplastic known for its strength of low friction, dimensional stability, and POM is a critical material in an industry ranging from automotive to consumer electronics. Furthermore, its unique characteristic of sustaining performance under challenging condition makes POM more crucial. In this article, I will discuss POM’s Material properties as well as its use in novel POM in design and manufacturing. Knowing them will help engineers, product designers and material scientist to choose wisely depending on need of specific application. Thus, I encourage you to explore the features that define POM and deeper into its potential performance.
What Are the Mechanical Properties of the POM Material?
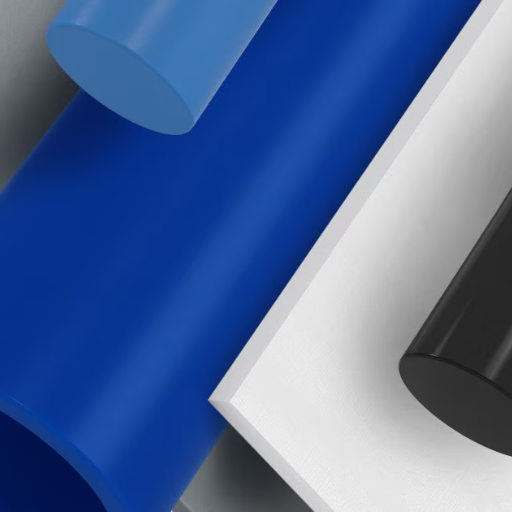
POM is well known for its remarkable characteristics of mechanical properties, furthermore, with all of them combined they provide greater reliability in manufacturing.
- High Strength and Stiffness: As POM also shows a significant amount of tensile strength, its rigidity allows POM to take heavy loads and keep its shape and strength during the stressful situations.
- Low Friction and Wear Resistance: POM gears and bearings benefit from natural low friction wear resistance as well as high durability for wear and tear.
- Dimensional Stability: Even with prolonged mechanical stress and temperature changes, POM retains its dimensions and resist deformation.
- Fatigue Resistance: The material exhibits remarkable capability with enduring repeated cyclic loading, ensuring reliability in dynamic applications.
- Impact Resistance: To sudden impacts, POM demonstrate a level of resilience, therefore is useful in harsh working conditions.
These properties make POM critical where strength, precision, and durability are needed.
How does hardness affect POM plastic?
The deformation characteristic of POM plastic plays a crucial role in determining its performance attributes in different use cases. Hardness improves surface protection against wear and abrasion, making it easier for frequently used items like gears and bearings to see less damage. It also helps protect its shape and strength during mechanical load within normal operating range, having a very low chance of any permanent change in geometry with time. On the other hand, highly hard materials can lower the ability to resist impacts by making them more rigid and through energy absorption from sudden shocks. The balance of higher hardness along with elastic range of deformation is why POM is highly in demand for engineering applications.
What is the tensile strength of polyoxymethylene?
Depending on the grade and composition of the polyoxymethylene (POM) material, its tensile strength may vary from 60 to 70MPa (megapascals). Exhibiting a more crystalline structure than copolymers, Acetal homopolymers, which form a purer version of POM, exhibit greater tensile strength than copolymers. Strength characteristics provide immense value when greater tensile strength is needed without any permanent damage. However, POM’s tensile strength can be affected by factors like temperature and humidity, illustrating the fundamental need of specific grades for certain engineering tasks.
How does impact strength compare in acetal and POM?
The impact strength of these acetal homopolymers(POM-H) and copolymers (POM-C) sharply differ due to varying molecular structures and grades used. Stiffer materials usually offer better impact resistance, and so homopolymer acetals tend to perform better due to their higher degree of crystallinity – at least until a threshold when repeated sudden impact and even temperature causes brittleness, like what is often the case with POM-H.
On the contrary, copolymer acetal is usually more ductile and shows greater resistance to heat and oxidative aging degradation. In turn, this enhanced chemical stability provides better performance for applications subjected to varying environmental conditions, as well as slightly improved impact resistance under dynamic loads. Precise impact strength values are often provided by manufacturers in terms of energy absorbed (e.g. kJ/m²) to allow selection of materials for rigorous engineering systems. While choosing between homopolymer and copolymer acetals, the operational environment and the stress factors greatly influence the decision.
What Are the Properties of POM that Make it Unique?
Due to its diversity in chemical structure and composition, polyoxymethylene, otherwise known POM, is noted for possessing good mechanical combination. POM has durable strength and high stiffness which further assists in demanding rigidity, thus, precision parts can be engineered easily. Unlike other materials, POM does not wear off and is creep resistant which means it withstands enduring mechanical pressure. POM is also said to offer low friction and a self-lubricating trait, making components with moving parts easier to manage. While having these primary attributes, POM also proves resistant to moisture, solvents, and numerous chemicals making it easier to work with. Such a blend of characteristics makes POM desired in dealing with materials for automotive and consumer good industries.
What are the thermal properties of POM plastic?
POM plastic, also referred to as polyoxymethylene plastic, has remarkable properties of heat that aid in its numerous industrial applications. It has a maximum continuous use temperature of 176°F to 212°F (80°C to 100°C) utilizing. POM exhibits superior dimensional stability at low and high temperatures, ensuring consistent performance in thermal cycling conditions. Mathematically, it is well suited for applications which have a high frequency of use. Its maximal heating frequency also retains, 329 °F to 347 °F (165 °C to 175°C) alongside the previously stated temperatures. Also, moderate amounts of heat allow it to retain its mechanical strength and stiffness; these features, alongside low thermal conductivity, make it optimal in insulating components. Coupled with lack of mechanical inefficiencies during moderate heats alongside no transfer, these extreme performance features prove its usage in high-end environments.
How does chemical resistance play a role in POM applications?
Polyoxymethylene (POM) is advanced engineering thermoplastic which has outstanding chemical resistance to fuels, solvents, oils, and hydrocarbons, greatly broadening its use in different industries. Because POM parts are exposed to severe chemical environments, for instance, in chemical processing equipment or in fuel system parts, they need to maintain their integrity and mechanical strength. In addition, POM is used in plumbing fixtures and water-handling systems because hydrolysis does not lower the polymer’s efficiency in humid and aqueous conditions. Chemically hostile environments enable POM to increase maintenance intervals and reduce costs, thus widening its usage in industries with aggressive chemicals and needing resilience and durability.
What is the significance of dimensional stability in POM resin?
The dimensional stability of POM resin describes a critical property that is important in the preservation of the accuracy of the shape, size, and tolerances of the material during mechanical and thermal stress. It is important in high-precision engineering such as in gears, bearings, and in automotive components. In these areas, the POM’s low thermal expansion whilst maintaining its shape improves performance at high temperatures and makes it suitable to areas require sustaining thermal requirements, as well as minimizing deformation. High resistance protects against long term exposure to moisture, preventing such materials from swelling or warping during assembly. Dimensional stability reduces mechanical failure whilst widening the useful range of other engineering polymers in hybrid systems for industries with precise engineering needs.
What Are the Different Grades of POM and Their Uses?
Polyoxymethylene (POM) is available in two primary grades:
- Homopolymer POM
This grade is used for applications with greater mechanical precision like slow moving parts such as gears, bearings and conveyor elements. With POM copolymer materials, this grade has greater strength, stiffness, and resistance to chemical corrosion.
- Copolymer POM
Copolymer grades are best for products which require thermal stability under moist conditions or hydrolysis and alkaline environments such as fuel systems for cars, plumbing devices, or electric components.
Meeting the specified requirements for a given performance for an industrial application is made possible with the precise engineering of each grade.
What distinguishes POM homopolymer from POM copolymer?
Differences in industrial use are mainly attributed to molecular structure and other characteristics of POM homopolymer and POM copolymer. Unlike its copolymer counterpart, POM homopolymer is made of uniform polyoxymethylene chains which make it more mechanically strong, rigid and harder. Its higher crystallinity increases its wear and creep resistance, though it can lead to greater brittleness and thermal instability under prolonged heating.
The POM copolymer has a structure with some incorporated comonomers which are known to reduce crystallinity otherwise enhancing thermal stability along with other degradation resistances significantly. These specific properties make copolymers particularly advantageous in environments with fluctuating temperatures or where exposure to moisture and chemicals is possible. In addition, POM copolymer has lower porosity compared to homopolymer grades which decreases formaldehyde emissions, important for use in sensitive emissions applications.
Which POM grades are best for high-performance applications?
How is Polyoxymethylene Used in Engineering Thermoplastics?
Polyoxymethylene (POM) is widely used in engineering thermoplastics for its excellent mechanical properties, dimensional stability, and low friction. It is commonly applied in industries such as automotive, electronics, and consumer products to manufacture precision components like gears, bearings, and housing parts. POM’s ability to resist wear, moisture, and chemicals makes it ideal for environments requiring durability and reliability. Its ease of molding also enables the production of intricate and consistent parts, crucial for high-performance applications.
What industries benefit from the use of POM plastic?
POM plastic serves a critical purpose in diverse sectors due to its exceptional mechanical strength and dependability. In the automotive industry, POM is used extensively for fuel system components, seat belt systems, and wear resistant interior parts. Similarly, the electronics industry uses POM for precision parts such as connectors, switches, and housings owing to POM’s wonderful insulating characteristics. Moreover, the medical industry uses POM biocompatible plastics for inhalers, surgical instruments, and other precision medical devices that need stringent biocompatibility. Its use is also dominant in the consumer sector for manufacturing zippers, fasteners, and components for household appliances. POM is preferred for these operations because of its reliability against physical deformation, endurance under extreme temperatures, and stability over prolonged periods.
How does POM compare to other engineering plastics?
Key Point |
POM (Polyoxymethylene) |
Nylon (PA) |
ABS (Acrylonitrile Butadiene Styrene) |
Polycarbonate (PC) |
PTFE (Polytetrafluoroethylene) |
PEEK (Polyether Ether Ketone) |
---|---|---|---|---|---|---|
Tensile Strength |
High |
Moderate to High |
Moderate |
High |
Low |
Very High |
Flexural Strength |
High |
Moderate to High |
Low |
High |
Low |
Very High |
Temperature Resistance |
Up to ~100°C |
Up to ~120°C |
Up to ~85°C |
Up to ~135°C |
Up to ~260°C |
Up to ~250°C |
Wear Resistance |
Excellent |
Good |
Moderate |
Good |
Excellent |
Excellent |
Impact Resistance |
Moderate |
Moderate to High |
High |
Very High |
Moderate |
High |
Moisture Absorption |
Low |
High |
Low |
Low |
None |
Low |
Chemical Resistance |
High |
Moderate |
Moderate |
Moderate |
Excellent |
Excellent |
Electrical Insulation |
High |
Moderate |
High |
Good |
Excellent |
Good |
Machinability |
Easy |
Moderate |
Easy |
Moderate |
Difficult |
Difficult |
Cost |
Moderate |
Low |
Low |
Moderate |
High |
Very High |
What are the common applications of POM in manufacturing?
POM a polyoxymethylene or acetal is an engineering plastic used in manufacturing because it is tough and resistant to wear. An overview of the POM application in engineering manufacturing is presented below.
- Gear Mechanisms
POM is commonly used in manufacturing auto and consumer product components such as gears. Its low friction coefficient, excellent wear resistance, alongside high mechanical strength makes POM ideal for moving parts; timing gears and small precision gear trains in household appliances serve as example.
- Precision Components
The wear, machinability, and shape keeping properties of POM apply towards its use in precision component parts bushings, bearings, and even valve seats especially in cases where moisture absorption and solvent exposure is limited.
- Automotive Parts
The application of POM is extensive in the automotive industry for fuel system parts like fuel caps and pump parts, as well as door locks, fuel windows, and clips. Its use is extremely valuable for the automotive industry because of its exposure to harsh environment oil, fuel, and high temperature.
- Electrical and Electronics
POM is also frequently employed for manufacturing small mechanical parts, connectors, and housings of electronic devices due to the device’s electrical insulation characteristic. It can also be depended on as a material for long term stable circuit board components and precision connectors.
- Consumer Goods
Fasteners, zippers, curtain tracks, and parts of sports equipment like ski bindings and pedals of bicycles are some consumer goods products which utilize POM due to its aesthetic, rigidity and strength features.
Withstanding numerous industry standards and being able to fulfill almost any manufacturing need, POM proves to be remarkably efficient as an engineering material. Its sheer usage across multiple industries showcases its immense noteworthy influence in boosting innovative functionality.
What Makes POM a Preferred Choice in Engineering?
Increasingly used in all branches of engineering, POM has exceptional mechanical properties, and due to its broad use in all engineering disciplines, such as automotive precision parts, guarantee strength and impact resistance. It has low friction, POM provides dimensional stability and retention of its shape which is ideal for minimized wear, moisture corrosion, and a range of chemicals. With all of these advantages, POM is becoming an ideal material for many industrial and domestic products.
How does rigidity contribute to the performance of POM?
As a characteristic of POM, rigidity supports its effectiveness in more challenging applications. Stiffness of this material enables retention of shape amid load due to considerable stress for gears, bearings, and other structural parts. Its natural stiffness guarantees POM’s lack of significant deformation or deflection due to static and dynamic stress over time, which assists in the preservation of essential mechanical tolerances and optimal mechanical performance in multi-part systems. In addition, rigidity ascribed to POM aids in absorbing and enduring changing mechanical loads throughout its duration of use asymmetrically to the rate of material degradation, extending component life and ensuring stable functioning in multiple industries and business applications.
What is the melting point of POM and its implications?
The melting point for Polyoxymethylene(POM) is around 162℃ to 175℃ (324° to 347°F) depending on the formulation and specific grade. The high temperature is attributed to its structure and how it is mechanically strong and thermally stable. POM is used in demanding manufacturing situations such as auto parts, electrical insulators, and industrial complex machines due to high precision and durability. However, near its melting point, extra care for thermal management needs to be taken as it can result in deformation or loss of mechanical properties. As with any material, there is a need for optimal operational conditions to ensure the dispensation of POM works long term and strongly.
What are the electrical properties of POM plastic?
POM (Polyoxymethylene) has exceptional electrical characteristics relevant to the electrical and electronic fields. POM plastics have high dielectric strength which allows for withstanding strong electric fields without electrical breakdown. This is important for safety and reliability for insulating components. POM also has a low dielectric constant and low dissipation factor. This contributes to POM’s effectiveness in minimizing energy waste during electrical operations. Furthermore, POM shows good electrical insulation resistance, maintaining the integrity of critical applications. Together with its mechanical strength, POM is one of the preferred materials for connectors, insulators, and precision electronic components.
Reference Sources
-
Bioactive Polyoxymethylene Composites: Titanium oxide nanoparticles provided the best antibacterial efficacy (100% against E. coli and 96% against S. aureus) without significantly altering mechanical properties.
-
Effect of POM Fiber on Ultra-High-Performance Concrete (UHPC): POM fibers enhanced UHPC’s mechanical properties, with optimal performance at 2% fiber content. POM outperformed other synthetic fibers like polypropylene and polyvinyl alcohol in toughness and durability.
-
POM/Graphene Nanocomposites for Tribo-Mechanical Applications: At 0.5% GNP loading, the composite showed a 51.3% increase in flexural modulus and a 40.6% reduction in wear rate under dry conditions.
Frequently Asked Questions (FAQs)
Q: What is Polyoxymethylene (POM) commonly known as?
A: Polyoxymethylene is commonly known as Delrin, which is a trademarked name for this acetal polymer.
Q: What are the key properties of POM material?
A: The key properties of POM material include good dimensional stability, high strength, low friction, and excellent wear resistance.
Q: How does POM exhibit good dimensional stability?
A: POM has good dimensional stability due to its low moisture absorption and high resistance to thermal expansion, allowing it to maintain its shape under varying conditions.
Q: In what applications is POM used due to its material properties?
A: POM is used in various applications such as automotive parts, consumer goods, and industrial components because of its excellent strength properties and versatile material characteristics.
Q: Can POM be modified for specific applications?
A: Yes, POM can be modified to enhance its properties, such as adding fillers or reinforcements to improve its mechanical properties and electrical insulation properties.
Q: What are the key advantages of using POM over other polymers?
A: The key advantages of using POM include its superior mechanical properties, good dimensional stability, low friction, and versatility as an engineering plastic.
Q: How does formaldehyde relate to POM?
A: POM is produced through a polymerization process that involves formaldehyde, which is a key raw material in the manufacturing of this acetal polymer.
Q: What makes POM a high-performance engineering plastic?
A: POM is characterized by its high strength, excellent wear resistance, and ability to perform well across a wide range of temperatures, making it a high-performance engineering plastic.
Q: What are the electrical insulation properties of POM?
A: POM exhibits good electrical insulation properties, which makes it suitable for use in electrical components and applications that require non-conductive materials.
Q: Why is POM considered a versatile engineering plastic?
A: POM is considered a versatile engineering plastic due to its combination of strength properties, good dimensional stability, and adaptability to various manufacturing processes, making it suitable for diverse applications.