Polyoxymethylene (POM) also called acetal and Delrin® is an engineering polymer used widely across different industries as its mechanical properties are favorable. POM holds significance in areas such as aerospace, automotive, consumer goods, and electronics. Because of its use across multimodal sectors, it raises a question: what is POM plastic and what makes it favorable for such enormous precision and reliability demands? This article serves as a comprehensive guide containing an overview of POM’s structure, characteristics, manufacturing processes, and applications. Suppose you’re a materials engineer, a product designer, or even interested in sophisticated polymers. In that case, this article will explain in detail how and why POM is still an important asset in modern engineering and innovation.
What Are the Applications of POM Plastic?
Polyoxymethylene (POM) plastic is one of the most preferred polymers in the automotive and industrial sectors, primarily due to its excellent strength, stiffness, low friction, and reduced warping. It can be found in gears, valves, bearings, and other industry-sharp precision parts. POM also finds good use in electrical parts such as plugs and switches owing to its good insulation and low wear properties. Moreover, POM is chemically resistant and very durable, which is why it is used in consumer products such as zippers, fasteners, and kitchen utensils. These features enable POM to be widely used in situations where high dependability and accuracy is essential.
How is POM Used in the Automotive Industry?
The automotive sector benefits significantly from POM’s utilities. It is leveraged mechanically for its strength, dimensional stability, low friction, and in serving other industry functions. It is famous for precision manufacture of gear wheels, bearings, and sliding mechanisms, where superlative wear resistance is crucial during continuous operation. Under the hood of an automobile, POM is utilized in fuel system components, cooling system elements, and electrical housings. These parts need to operate in harsh conditions encountering high moisture and temperatures. POM’s low moisture absorption and high temperature resistance makes it sustain fuel, oil, and grease exposure which is essential to its use in demanding automotive environments. Parts that require the dynamic stress under high temperature incurs POM useful in safety critical systems such as seatbelt assemblies and locking mechanisms preserving accuracy in decades to come for modern automotive structures.
What Are the Common Applications of POM Material?
POM is a remarkably intermediate thermoplastic withstanding a variety of industries and applications which require exceptional engineering properties such as high mechanical strength, high chemical resistance, and further destructive factors. Here’s a detailed guiding list of several everyday applications of POM materials:
- Automotive Components
-
- Fuel System Parts: Fuel caps, fuel pumps, and valve components are manufactured from POM due to its primary acceptance for fuels and oils.
- Seatbelt Assemblies: These products offer safety and also effectively endure wear and harsh conditions over an extended period of use. Deformation due to dynamic forces is not observed.
- Gears and Bearings: Its low coefficient of friction and high wear resistance makes it ideal for use on moving parts.
- Industrial Machinery
- Gear Wheels and Conveyor Systems: They ease motion transmission and are known for their proper functioning under harsh conditions.
- Sliding and Rotating Components: These provide low friction surfaces which reduces wear and increases lifespan of worn parts.
- Consumer Electronics
- Keyboard Switches: Gives a satisfying click sound and serves for a long time.
- Connectors and Housings: Provides stability of shape and accuracy which is important for precision electronics.
- Medical Devices
- Insulin Pens and Drug Delivery Systems: Has biocompatibility and does not change in a sterile environment, hence, is safe when used for drug delivery systems.
- Surgical Instruments: Tools requiring rigidity to perform withstand harsh chemicals and require durability.
- Household and Appliance Applications
- Kitchen Appliances: Used in the construction of some parts like gears and rollers which are found in dishwashers and are safe to wash in dishwashers.
- Water Fixtures and Plumbing: Has resistance to liquid and chlorine; thus, has long lasting usefulness.
Combining high strength, easy to work with, and environmental resistant, POM has shown its value across many industries.
What Are the Mechanical Properties of POM Plastic?
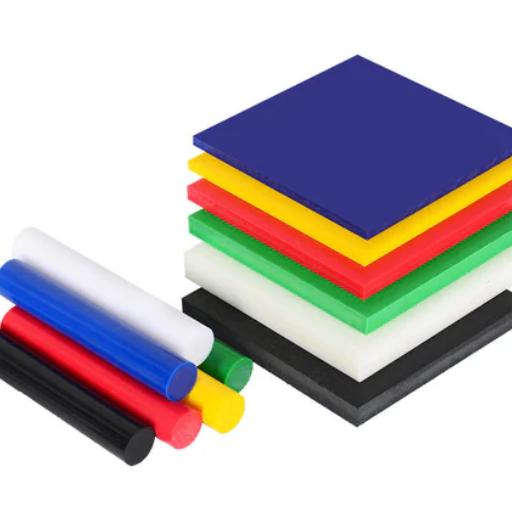
POM plastic or Polyoxymethylene showcases the unique blend of mechanical attributes which enables plastic to be highly applicable. They are:
- High Tensile Strength: POM sustains pulling forces without deformation or failure which surpasses considerable limits.
- Excellent Stiffness: The material keeps its shape and offers durability and structural strength in demanding applications.
- Low Friction: It has a naturally low friction coefficient which aids in smooth motion for sliding as well as rotatory participants like gears and bearings.
- Superior Dimensional Stability: POM experiences minimal warp or shape alterations when subjected to sustained loads or temperature variations.
- Impact Resistance: Energy absorbing capacity without breakage allows the polymer to be used in repeatedly forced or stressed parts.
These properties reinforce POM’s significance in precision engineering and industrial applications, alongside the wear and environmental factor endurance.
How Does POM Compare to Other Engineering Plastics?
Key Parameter |
POM (Polyoxymethylene) |
Nylon (Polyamide) |
ABS (Acrylonitrile Butadiene Styrene) |
PTFE (Polytetrafluoroethylene) |
---|---|---|---|---|
Tensile Strength |
High |
Moderate to High |
Moderate |
Low |
Dimensional Stability |
Excellent |
Good |
Moderate |
Exceptional |
Friction Coefficient |
Low |
Moderate |
High |
Ultra-Low |
Water Absorption |
Very Low |
High |
Low |
Negligible |
Temperature Resistance |
Up to 140°C |
Up to 120°C |
Up to 100°C |
Up to 260°C |
Impact Resistance |
High |
High |
Very High |
Low |
Chemical Resistance |
Excellent |
Good |
Moderate |
Excellent |
Ease of Machining |
Easy |
Moderate |
Easy |
Difficult |
Cost |
Moderate |
Low to Moderate |
Low |
High |
What Are the Dimensional Stability and Mechanical Strength of POM?
Polyoxymethylene (POM), often referred to as acetal, is acclaimed for having remarkable strength with superiority to other polymers for bearing and sliding precision mechanical parts. This engineering polymer surpasses in precision parts not only for robotics, but also in modeling machinery used in automobiles. Dimensional stability expresses the ability of a material to retain its shape and size when subjected to temperature, humidity, and mechanical loads or forces. Water retention is low with POM, therefore, eliminating any chances of noise and dimensional changes over years especially in the case with humid surroundings.
POM has strong tensile strength and extraordinary resistance to creep, making him stiff enough for POM to be useful in mechanical applications. These features facilitate the employment of POM in high-bearing applications like gears, bearings and even structural components. Moreover, POM performs well mechanically with temperature changes up to 140℃ for most types enabling him to perform in critical situations like servicing on an aircraft engine. This makes POM very important in the automotive, aerospace, and consumer electronics industries.
What Are the Thermal Properties of POM Plastic?
Thermoplastics have wide use in carving components like gears, conveyor belts, fuel and oil injectors, owing to their excellent resistance, low wear rate, and friction co-efficient. Polyoxymethylene (POM) is one of the widely accepted thermoplastics, being a good performer POM works wonders in heating applications as his softening point lies anywhere between 162℃ to 177℃. As well, its thermal stability in this range allows reliable functioning at moderate to high temperatures. Moreover, POM has a low coefficient of thermal expansion which secures further stability of dimensions and strength against thermal deformations during temperature changes.
POM shows a high heat deflection temperature (HDT) thermal performance, often cited around 120°C at 1.8MPa, just like some other materials, therefore it can be used on parts which bear loads in heated surroundings. POM also has other notable properties, including its low thermal conductivity, creating insulation benefits in certain applications. These thermal properties together with POM’s mechanical and chemical features strengthens its use in precision parts for automobiles, electrical appliances, and industrial equipment where thermally sensitive components require optimal performance.
How Does POM Plastic Ensure Good Dimensional Stability?
POM plastic also ensures good dimensional stability through low moisture absorption, high rigidity, and resistance to temperature changes or chemicals. POM’s low water absorption protects against the material from swelling or distortion, while rigidity aids retention of shape under compressive stress. Moreover, POM’s thermally stable character allows the material to perform within expectations at different temperatures, which is critical for elements that need machining on tight tolerances through passage of time, especially under varying conditions.
What Factors Contribute to the Dimensional Stability of POM?
The outstanding dimensional stability of polyoxymethylene (POM) is a result of its material properties and how it interacts with the surroundings. Shetland Oxford below sets forward some of the relevant writing factors:
- Low Water Absorption
Polyoxymethylene usually absorbs water within 0.2% in 24 hours under standard ambient conditions. This low absorption rate of POM aids in minimizing the distortion, swelling, or moisture-induced dimensional changes; thus, POM is suitable for consistent use in humid and wet applications.
- High Crystallinity
POM gains a crystallization degree of 65% to 75% depending on the specified grade as well as processing conditions. The high ordering of this structure increases hardness and rigidity which, in turn, decreases creep and deformation over time.
- Thermal Stability
The thermal stability of POM is of great significance for preserving shape over a wide-range temperatures, around -40°C to 120°C for standard grades. This enables consistent output across industrial applications requiring elevated temperatures.
- Low Thermal Expansion Coefficient
With a POM having a coefficient of linear thermal expansion (CLTE) value of 10-14 x 10^-5/°C, POM also thermally expands linearly. Compared to other thermoplastics, this value is comparatively low to most of them. Because precise measurements can be maintained, this value is highly useful.
Considering all of the factors, POM shows a remarkable ability to preserve dimensional accuracy and structural integrity in both static and dynamic environments, making it preferred for engineering applications demanding precision and reliability.
How Does the Dimensional Stability Affect POM Applications?
As with all POM’s engineering properties, its dimensional stability increases its effectiveness in many uses across different fields of engineering. This stability allows parts to retain accurate geometry even with changes in temperature, humidity, or mechanical strain. An example of this can be found in the automotive industry where POM is frequently used in gear drives and fuel system parts. With such precision in engineering, any change in size or shape, no matter how minute, can interfere with proper function or cause misalignment during assembly.
In consumer electronics, the low thermal expansion coefficient of the material also helps keep complicated parts safe from shifting out of place during prolonged use, leading to failure. Resistance to deformation makes POM equally ideal for producing medical equipment, which requires strict tolerances to ensure safety for the patient and effectiveness when in use. Thus, ease of manufacture aside, enhanced stability reduces material fatigue or misalignment in dynamic applications, leading to greater reliability and service life.
What Are the Different Grades of POM Plastic?
Polyoxymethylene (POM) plastics are commercially split into two primary grades:
- Homopolymer POM – This is produced with a single polymer chain which gives it high strength, stiffness, good chemical resistance and makes it easy to work with. It is best for precision and hight mechanical performance applications like bearings and gears.
- Copolymer POM – These types of grades added comonomers to the main chains which lowers the material’s density of crystallinity. Strengths include increased thermal stability and decreased hydrolysis, making them useful for automotive parts and plumbing components exposed to heat and water.
Formulation of each Grade can be modified by adding fillers, lubricants or other substances to improve face performance parameters such as wear resistance, ultraviolet stability and electric conductivity.
What Are the Characteristics of POM Homopolymer?
The increase in heat does not affect the molding of the polyoxymethylene homopolymer, as its rigidity, strength, and expansion are always on the positive side in industrial settings or outside. Belonging to the family of thermoplastic polymers, polyoxymethylene has an excellent ability to crystallize which supports the thermoplastic well. It allows it to slide and rotate parts. POM homopolymer is not limited to these features alone; being an excellent performer to several chemicals like warm acids, oils, solvents, and strong fuels gives it a huge tick in the industrial and automotive operations boxes. POM supports industry and allows workers an excellent performance in heavy-duty work. Though POM homopolymer is mostly used, POM works best under heavy compression and heat, allowing great flexibility. POM copolymers in comparison to POM homopolymers exhibit more resilience towards thermal and oxidative degradation.
How Do Different POM Grades Affect Performance?
The performance Of Polyoxymethylene (POM) is partially determined by the specific grade employed, as all grades are tailored to distinctive needs and conditions. As an example, homopolymer grades of POM are famous for their enhanced crystallinity which increases the tensile strength, stiffness, and the wear resistance. These characteristics enable effectiveness of the POM homopolymer grades in precision components which require high performance in mechanical properties such as gears and bearings.
POM copolymer grades, on the other hand, have remarkable resistance to hydrolysis, thermal oxidation, and alkaline conditions. Thus, POM is ideal for use in plumbing systems and automotive fuel systems which require long-term exposure to moisture and chemical agents. Moreover, some modified grades are even better in having glass fibers or lubricants added which provide extra benefits such as better dimensional stability, lower friction, and greater temperature resistance. The selection of grade is therefore critical so that it matches the requirements of the application for best results in performance.
What Is the Chemical Resistance of POM Plastic?
POM plastic, or polyoxymethylene/acetal, has good resistance against many chemicals. POM is protective of fuels, oils, solvents, and weak acids which makes it useful for applications where these substances are present. On the other hand, strong acids, bases, and oxidizing agents that may weaken the structure are more likely to damage POM. In surviving the exposure to chemicals, POM must be tested for the specific chemical environment it will face. The concentration of the chemicals can also affect response seeking compatibility to preserve performance integrity.
How Does POM Perform Against Various Chemicals?
The POM grade plastic possesses excellent resistance to a wide array of chemical compounds. This feature, coupled with its low costs, explains why it is so extensively used throughout multiple industries. POM is known to resist neutral salts, alcohols, and even aliphatic hydrocarbons as they do not affect its structure over time. Also, POM can withstand many esters and ketones which broadens its use significantly. Its shortcomings include exposure to strong mineral acids, concentrated alkalis, or oxidizing agents which will hydrolyze or oxidatively degrade POM. These processes will diminish mechanical features like tensile strength or volumetric stability over time.
The specific temperatures in question. Elevated temperatures are capable of fostering aggression in some chemicals and thus hasten the chemical degradation process. With e.g., POM plastic materials, mechanical and physical properties are related to concentration, operating conditions, and temperature. In practical tests, a POM’s steadfastness amid certain levels of aggression, up to a defined limit, is confirmed where POM should not be excessively chemically exposed. Proper selection and testing of POM components from POM ensure durability mechanical effectiveness and long-term industrial performance.
What Are the Limitations of POM’s Chemical Resistance?
While polyoxymethylene (POM) demonstrates excellent chemical resistance under many conditions, these limitations of POM’s performance require thorough consideration:
- Susceptibility to Strong Acids and Bases
POM has a weak resistance to strong acids and bases. The application of concentrated acids like sulfuric or hydrochloric acid, or strong bases, for instance sodium hydroxide, will cause hydrolysis or depolymerization damaging the polyoxymethylene mechanically and structurally. Research has shown that exposure to such environments with pH value lower than 4 or above 10 significantly reduces tensile strength.
- Compatibility with Halogenated Compounds
- Poor Performance at Elevated Temperatures with Chemicals
Thermal factors, especially aggressive chemicals, will diminish POM’s chemical resistance at higher temperatures. Over 80°C (176°F) POM is more susceptible to chemical attacks from certain alcohols and organic solvents that it would tolerate in lower temperatures.
- Limited Resistance to Oxidizing Agents
POM does poorly with strong oxidizing agents like nitric acid and hydrogen peroxide. These chemicals will compromise POM’s molecular structure thereby resulting in cracking or discoloration. Studies show that exposure to hydrogen peroxide over 10% concentration increases the likelihood of material fatigue – affecting how long the material can be used.
Addressing these protective coatings or optimized structural usage environments will enhance the reliability of POM components, even in harsh and challenging applications.
Reference Sources
-
Thermal Analysis of POM Pyrolysis: This study explores the pyrolysis and hydrothermal conversion of POM under various conditions. It highlights the kinetic advantages of hydrothermal methods over pyrolysis, showing reduced activation energy and improved degradation efficiency.
-
POM as a Soil Reinforcement Material: Researchers investigated using POM waste as granular columns to enhance the strength of soft clay soils. The study demonstrated significant improvements in soil stability and shear strength, promoting the use of recycled POM in geotechnical applications.
-
Chemical Upcycling of POM: A novel method was developed to upcycle POM waste into industrially relevant chemicals like dialkoxymethanes and cyclic aminals. This approach emphasizes sustainable chemical recycling and valorization of POM.
Frequently Asked Questions (FAQs)
Q: What is polyoxymethylene (POM) plastic material?
A: Polyoxymethylene, commonly known as POM, is an engineering thermoplastic that is widely used due to its excellent mechanical properties, dimensional stability, and low friction properties. It is often used in applications requiring high strength and precision.
Q: What are the advantages of POM?
A: The advantages of POM include its exceptional mechanical properties, good impact strength, low friction properties, and excellent dimensional stability. These features make POM suitable for a wide range of applications, particularly in the automotive and engineering sectors.
Q: What are some typical applications for injection-molded POM?
A: Applications for injection-molded POM include gears, bearings, automotive parts, and various components in household appliances. Its versatility as an engineering thermoplastic allows for a wide range of applications in different industries.
Q: What are the disadvantages of POM material?
A: The disadvantages of POM material include its susceptibility to hydrolysis, which can affect its performance in humid environments. Additionally, POM can be more expensive compared to other polymers, and it may not be suitable for very high-temperature applications.
Q: How does acetal compare to polyoxymethylene?
A: Acetal is another name for polyoxymethylene (POM), meaning they are essentially the same material. However, acetal is often used in reference to specific formulations or grades within the polyoxymethylene family, particularly in the context of acetal plastic applications.
Q: What makes POM suitable for engineering applications?
A: POM’s excellent mechanical properties, combined with its low friction properties and dimensional stability, make it a versatile engineering plastic. These characteristics allow POM parts to perform reliably in demanding conditions, making it a preferred choice among engineers.
Q: What are the electrical properties of acetal polymer?
A: Acetal polymers generally exhibit good electrical properties, making them suitable for applications involving electrical insulation. They have low moisture absorption, which helps maintain their electrical performance in various conditions.
Q: Can you explain the range of applications for POM?
A: POM is widely used in many applications, including automotive components, consumer goods, industrial machinery, and medical devices. Its versatility allows it to be molded into intricate shapes, making it ideal for various industries.
Q: What are the advantages and disadvantages of POM?
A: The advantages of POM include its excellent mechanical properties, good impact strength, and versatility in applications. However, the disadvantages of POM material include its sensitivity to moisture and potential hydrolysis, as well as a higher cost compared to some other polymers.